The Importance of a CNC Machine Shop
A CNC machine shop is a great choice for businesses and individuals who need to produce precision parts or prototypes. If you’re in the process of designing a new product and are unsure of how to produce it, outsourcing the process can be a good option. CNC machines allow for much more accurate and efficient production than manual machining methods.
Precision machining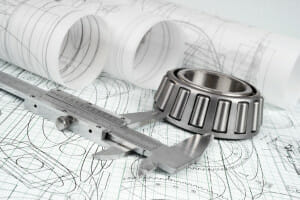
CNC machine shops, like Bates Machine and Mfg in Farmersville, TX, are a valuable resource for companies seeking precision machining services. Whether a company needs a single component or a complex component made of many parts, they can provide quality CNC machining services. With the help of these shops, businesses can reduce the cost of production and achieve higher productivity. Moreover, these machining companies also offer emergency machining services.
Precision CNC machining is a high-volume process that can produce a wide range of parts with a high degree of accuracy and tolerance. Its flexibility allows it to handle a variety of materials and plastics. This flexibility makes it a perfect choice for many industries.
Drill presses
Drill presses are a crucial part of any CNC machine shop. These high-tech machines feature a vertical spindle, a chuck, a clamp, and a feed lever that controls the depth and speed of the drill bit. They also allow users to add lubricant and coolant to ensure smooth drilling. Drill presses are also more accurate and provide greater power than handheld drills.
Drill presses are also useful for punching holes. When a mill is not equipped with a quill, a drill press is needed for this second operation. In addition to drilling, drill presses can also tap.
Milling machines
Milling machines in CNC machine shops are often used to manufacture small parts. They can be used to mill gears and gear teeth or to form flat surfaces. These machines use different kinds of cutting tools depending on the task that they are used for. Typically, milling machines produce parts that are within a tolerance of 5 mm. One millimeter is equal to 1/24500 inch. Modern CNC machine shops have quality control teams that make it a point to maintain this tolerance. This saves time and resources and benefits the customer.
Milling machines were first used as production machines. Whitney’s machine, for example, was the first milling machine, but it did not allow the knee to move vertically. It assumed that the part design had been previously set on the milling machine, so the vertical position was not necessary for each successive part. Early milling machines were primarily designed as production machines and did not require precise vertical positioning.
Optical inspection
Optical inspection in CNC machine shops uses different metrology tools to determine the overall quality and accuracy of a component. Typically, a surface plate is used for vertical measurements. These plates must be calibrated and maintain their shape. Granite is a popular choice for these surfaces. Optical inspection tools can be installed directly on a CNC machine or in a test room.
Optical inspection tools are generally affordable and easy to use. They can also be used in the shop floor and should be integrated into the workflow of machine operators. The equipment should include go/no-go gages and appropriate work instructions. The data from these measurements should be recorded digitally.
Maintenance schedules
A maintenance schedule for CNC machine shops is a critical part of ensuring the continued uptime and output efficiencies of a machine shop. In addition, it can improve profits by preventing unexpected breakdowns. Unplanned downtime can cost a factory anywhere from five to twenty percent of its total productivity. Unfortunately, six out of seven shops continue to run their machines to failure despite the potential benefits.
Maintenance schedules for CNC machine shops should be aligned with the use of the equipment. If maintenance is planned at the right intervals, it will not disrupt production. By incorporating a worker check system, the schedule can be based on availability and usage patterns to reduce costs and unnecessary downtime.